Richard Kassner
New member
Hello All,
I need advice from experienced boat builders. I am attaching a skeg to a Merrymeeting Bay Gunning Float. Below are the relevant particulars:
The Skeg is 3/4 inches thick, 26 inches long, and as tall as 3 3/4 inches. It is made of quatersawn white oak.
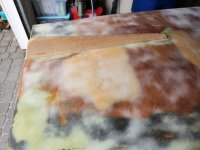
The Hull is 5/16th inches thick and made of cedar strips laminated in fiberglass. The hull has been faired with epoxy, micro-balloons, 3M Glass Bubbles, &TotalFair. I used a 1/16th inch drill bit and drilled 5 small pilot holes through the hull.
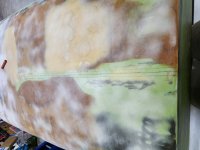
I have #10 Philips Flat Head Wood Screws made of Stainless Steel 316. They range in size from 3" to 1". These screw Heads are 1/8" long. The screw Shanks range from 5/8" to 1/8." The Major Thread Diameter is 3/16". The Counter Sink size is 7/16". Below is a picture with 5 of them up against the Skeg.
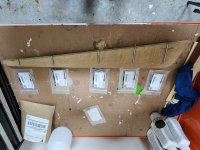
I watched a video where the host glued a skeg to a dory using Polysulfide before screwing the skeg to the hull. I understand that Polysulfide provides a person the ability to remove the skeg in the future without too much effort unlike some Polyurethanes like 3M 5200 or Epoxy Resin.
I know that I can prevent leaks if I attach the Skeg with Epoxy Resin and make a Fillet between the Skeg and the Hull. However, if the Skeg gets damaged, replacing the Skeg will be very difficult by removing the Epoxy Resin and Fillets.
Questions:
1. Are "some" of Screws that I plan to use too long or are longer Screws best for this application? (I am planning on using a drill press to pre-drill the holes but I am concerned about getting long screws with a 3/16" diameter in a 3/4 " wide piece of hard White Oak. )
2. Should I use Stainless Steel 316 "Finishing Washers" to seat the Screw Head? (I am concerned about sinking the 1/8" long Screw Head into the hull given that the Hull is 5/16" thick and the cedar strips are thin. However, I realize that the Finishing Washers will cause the Screw Head to stand proud inside the boat.)
3. Is the Polysulfide (like BoatLife Life-Caulk) a good idea or should I use 3M 4200 (not 5200) or is Dolfinite 2005N Natural Bedding Compound O.K. for this purpose? (I have the Dolfinite but never have used it.)
4. Would it be a good idea to drill 3/16" holes through the Hull to accommodate the Major Thread Diameter of the Screws even if 2 of the shorter Screws have Shanks shorter than the 5/16" Hull? (I am concerned about leaks but I am concerned about Screw threads damaging the Hull.)
5. Or should I just Epoxy the Skeg in with Fillets and forgo the Screws all together? (Forget about the idea of being able to remove the Skeg easiest should it get damaged.)
Any insights would be most welcome. Thanks in advance.
I need advice from experienced boat builders. I am attaching a skeg to a Merrymeeting Bay Gunning Float. Below are the relevant particulars:
The Skeg is 3/4 inches thick, 26 inches long, and as tall as 3 3/4 inches. It is made of quatersawn white oak.
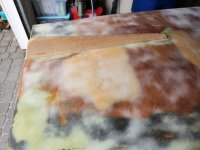
The Hull is 5/16th inches thick and made of cedar strips laminated in fiberglass. The hull has been faired with epoxy, micro-balloons, 3M Glass Bubbles, &TotalFair. I used a 1/16th inch drill bit and drilled 5 small pilot holes through the hull.
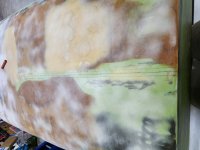
I have #10 Philips Flat Head Wood Screws made of Stainless Steel 316. They range in size from 3" to 1". These screw Heads are 1/8" long. The screw Shanks range from 5/8" to 1/8." The Major Thread Diameter is 3/16". The Counter Sink size is 7/16". Below is a picture with 5 of them up against the Skeg.
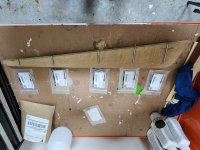
I watched a video where the host glued a skeg to a dory using Polysulfide before screwing the skeg to the hull. I understand that Polysulfide provides a person the ability to remove the skeg in the future without too much effort unlike some Polyurethanes like 3M 5200 or Epoxy Resin.
I know that I can prevent leaks if I attach the Skeg with Epoxy Resin and make a Fillet between the Skeg and the Hull. However, if the Skeg gets damaged, replacing the Skeg will be very difficult by removing the Epoxy Resin and Fillets.
Questions:
1. Are "some" of Screws that I plan to use too long or are longer Screws best for this application? (I am planning on using a drill press to pre-drill the holes but I am concerned about getting long screws with a 3/16" diameter in a 3/4 " wide piece of hard White Oak. )
2. Should I use Stainless Steel 316 "Finishing Washers" to seat the Screw Head? (I am concerned about sinking the 1/8" long Screw Head into the hull given that the Hull is 5/16" thick and the cedar strips are thin. However, I realize that the Finishing Washers will cause the Screw Head to stand proud inside the boat.)
3. Is the Polysulfide (like BoatLife Life-Caulk) a good idea or should I use 3M 4200 (not 5200) or is Dolfinite 2005N Natural Bedding Compound O.K. for this purpose? (I have the Dolfinite but never have used it.)
4. Would it be a good idea to drill 3/16" holes through the Hull to accommodate the Major Thread Diameter of the Screws even if 2 of the shorter Screws have Shanks shorter than the 5/16" Hull? (I am concerned about leaks but I am concerned about Screw threads damaging the Hull.)
5. Or should I just Epoxy the Skeg in with Fillets and forgo the Screws all together? (Forget about the idea of being able to remove the Skeg easiest should it get damaged.)
Any insights would be most welcome. Thanks in advance.
Last edited: