michael barnes
Active member
some of ya know, the previous owner of my boat replaced about 8 bolts in the transom of my starcraft with steel bolts, and they corroded all around each hole. the corners of my transom are fine, and the 3 triangular braces at the bottom are very solid, so i think ive got plenty to work with. the total thickness of the transom originally was 1.5" plus about .125" for the aluminum. so i have 2 questions
1) should i run a 6" wide strip of aluminum across the transom, to cover the eaten up bolt holes, and put two sheets of .75 plywood on the inside like it was originally?
or could i put a sheet of .75" plywood on the inside, then one on the outside, sandwiching the the aluminum transom, and use big washers around the bolt heads and nuts? i would like to keep it as cheap as possible, but i want it to work.
2) what should i use for bolts to avoid anymore corrosion?
thanks, mike.
starboard side
port side
the large holes are from a copper tube put in for a bilge pump hose.
the entire transom has pitting and corrosion, but around the bolt holes is where it is worse.
1) should i run a 6" wide strip of aluminum across the transom, to cover the eaten up bolt holes, and put two sheets of .75 plywood on the inside like it was originally?
or could i put a sheet of .75" plywood on the inside, then one on the outside, sandwiching the the aluminum transom, and use big washers around the bolt heads and nuts? i would like to keep it as cheap as possible, but i want it to work.
2) what should i use for bolts to avoid anymore corrosion?
thanks, mike.
starboard side

port side
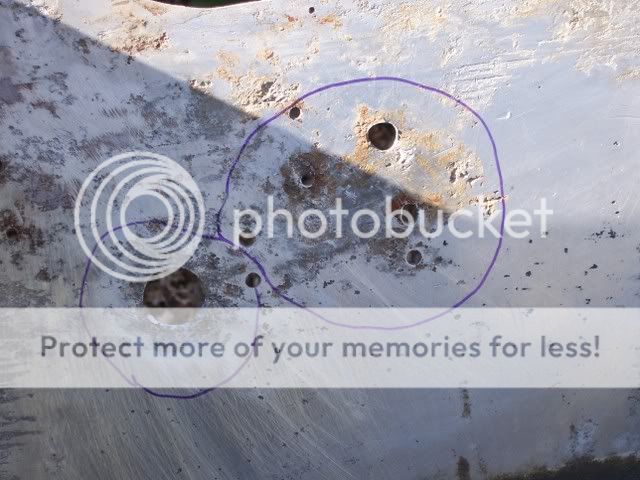
the large holes are from a copper tube put in for a bilge pump hose.
the entire transom has pitting and corrosion, but around the bolt holes is where it is worse.
Last edited: