Mark W
Well-known member
I caught the bug when I saw the postings about the min mud motor and after much discussion between Ed L, Tom Scholberg, Mark Cheney, "Ripped Off's" plans from another forum, John O'Neal, and others, I had to try to build one just for the fun of it. Will it work, who knows. It did give me something to do these past few weeks and I met some great people along the way. Here are some pictures of the motor. All that is left is to connect the prop when it arrives, machining the 3/8" drive shaft to fit into the weed whacker motor, hook up the throttle, attach the tiller, and put on the motor mount. Nothing too hard.
Here is a picture of Tom helping me out in his shop at school. Good thing I was there to help him out or this motor shaft would not have been finished.
Here is a shot of the motor after the shaft has been coated with a 3M Rubberized undercoating product. this should hold up well as it is used to paint the wheel wells of cars.
Hope it works out. Sorry about the picture quality, you can't get good photo's on the cell phone.
Mark W
Here is a picture of Tom helping me out in his shop at school. Good thing I was there to help him out or this motor shaft would not have been finished.
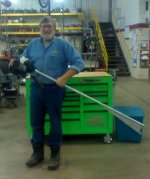
Here is a shot of the motor after the shaft has been coated with a 3M Rubberized undercoating product. this should hold up well as it is used to paint the wheel wells of cars.
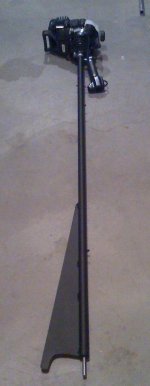
Hope it works out. Sorry about the picture quality, you can't get good photo's on the cell phone.
Mark W
Last edited: