Noah Shaver
Member
Good morning all, proud to say that this weekend I became the new owner of a 1993 TDB Classic 14. I picked this boat up from a true gentleman of a duck hunter in Central Pennsylvania that was a pleasure to deal with. He was very up front with the history and story of the boat and the condition.
This is not a boat that sat in a garage, this boat was hunted in multiple states over its lifetime. He has some awesome stories and pictures from the 90's and early 2000's hunting out of this boat. The "catch" so to speak is the fiberglass patch in the bottom of the boat. The purchase price was right, so we made the trip and plan to bring the boat back to her former glory.
In 1995 he was pulling the boat out of the water and somehow the hull came off the trailer and hit the pavement. It cracked the bottom layer of fiberglass at the rear of the hull near the transom. He admitted that he had plans to hunt the next day, so the patch was done overnight. He cut a square out of the bottom of the hull, replaced the plywood, and fiberglassed it over. Fast forward to present day and the patch fell out while sitting on the trailer. The boat has not been in the water in 8 years.
The square that he cut now needs to be patched again. I have taken a screwdriver to the surrounding plywood and everything is very solid. The plywood he used for the patch is rotted away, but the plywood used to construct the boat is very structurally sound. The transom and floor are also solid. The patch area is about 5" x 5".
I am by no means a fiberglass man, but I have a friend who has experience with it. We would like to patch this area and get this boat back on the water. What do you guys recommend as a method of repair for this and what materials do you recommend? Details on how many layers of glass, what weight of cloth etc are very much appreciated.
Thank you!
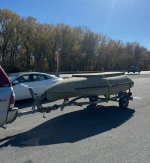
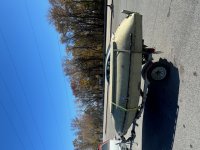
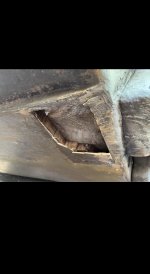
This is not a boat that sat in a garage, this boat was hunted in multiple states over its lifetime. He has some awesome stories and pictures from the 90's and early 2000's hunting out of this boat. The "catch" so to speak is the fiberglass patch in the bottom of the boat. The purchase price was right, so we made the trip and plan to bring the boat back to her former glory.
In 1995 he was pulling the boat out of the water and somehow the hull came off the trailer and hit the pavement. It cracked the bottom layer of fiberglass at the rear of the hull near the transom. He admitted that he had plans to hunt the next day, so the patch was done overnight. He cut a square out of the bottom of the hull, replaced the plywood, and fiberglassed it over. Fast forward to present day and the patch fell out while sitting on the trailer. The boat has not been in the water in 8 years.
The square that he cut now needs to be patched again. I have taken a screwdriver to the surrounding plywood and everything is very solid. The plywood he used for the patch is rotted away, but the plywood used to construct the boat is very structurally sound. The transom and floor are also solid. The patch area is about 5" x 5".
I am by no means a fiberglass man, but I have a friend who has experience with it. We would like to patch this area and get this boat back on the water. What do you guys recommend as a method of repair for this and what materials do you recommend? Details on how many layers of glass, what weight of cloth etc are very much appreciated.
Thank you!
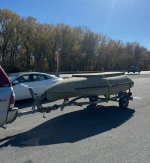
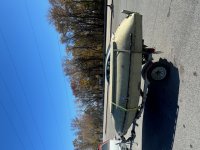
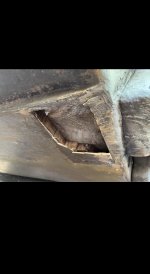