Richard Kassner
New member
Hello All,
I was thinking of steam bending 1/2 or 3/4 inch thick Quarter-swan White Oak planks over a boat's hull to add a keel and strakes to that boat. The planks maybe as much as 1 1/2 inches wide. I was planning to use epoxy to attach the plank to the boat's hull. I have never done this before.
I have watched some videos of people steam bending wood but not in the way that I think I can do so on this hull.
My question is as follows:
Is it feasible to tighten ratchet straps over a boat's hull with thin steamed wood planks so as to bend those steamed wood planks to conform to the surface of a boat's hull WITHOUT screwing the steamed wood planks into the hull?
Below is a picture of the boat's hull. (The gray color is NOT primer or paint but colorant added to protective epoxy barrier coats.)
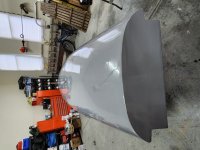
Below is a picture of the ratchet straps I was planning to use to compress the steamed wood plank over the hull.
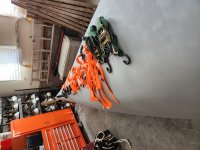
The general curve of the hull is rather gradual; however, one of the challenges is a hump or bulb at the bow that creates a sharpish curve. (I gather this hump or bulb was done to protect the rest of the hull when beaching the boat.) Therefore, I will probably have to cut away part of the plank so that the end of the plank meets the top of the hump or bulb.
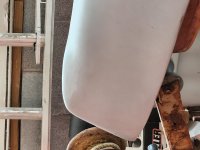
I would use epoxy and fairing compound to make everything appear uniform at the hump or bulb. I would use epoxy to fasten the wooden plank ( the keel and hull strakes) to the hull. I would use ratchet straps to hold these steam bent pieces of wood to the hull while the epoxy cures.
In sum, I would use the ratchet straps to bend the steamed wood and then use the ratchet straps to hold the bent wood onto the hull while the epoxy cured.
Again, is this idea feasible or will the force to bend the steamed wood be too great for ratchet straps to achieve?
Will the wood want to spring back some after bending it so that attempting to epoxy curved wood under the pressure of the ratchet straps be unfeasible?
I am reluctant to screw the wood planks into the hull because of potential leaks. Moreover, the hull is only 5/16ths of the an inch thick. This brings another question to mind.
Would such a hull be strong enough to accommodate the force of tightening down the ratchet straps to bend 1/2 to 3/4 inch thick White Oak?
I believe I have to use wood that has not been kiln dried and I have access to non kiln dried wood.
If it is an unreasonable to steam bend wood with ratchet straps that is O.K.. As I said I have never done this before.
Any insights would be most welcome.
I was thinking of steam bending 1/2 or 3/4 inch thick Quarter-swan White Oak planks over a boat's hull to add a keel and strakes to that boat. The planks maybe as much as 1 1/2 inches wide. I was planning to use epoxy to attach the plank to the boat's hull. I have never done this before.
I have watched some videos of people steam bending wood but not in the way that I think I can do so on this hull.
My question is as follows:
Is it feasible to tighten ratchet straps over a boat's hull with thin steamed wood planks so as to bend those steamed wood planks to conform to the surface of a boat's hull WITHOUT screwing the steamed wood planks into the hull?
Below is a picture of the boat's hull. (The gray color is NOT primer or paint but colorant added to protective epoxy barrier coats.)
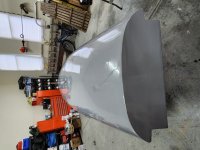
Below is a picture of the ratchet straps I was planning to use to compress the steamed wood plank over the hull.
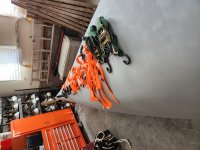
The general curve of the hull is rather gradual; however, one of the challenges is a hump or bulb at the bow that creates a sharpish curve. (I gather this hump or bulb was done to protect the rest of the hull when beaching the boat.) Therefore, I will probably have to cut away part of the plank so that the end of the plank meets the top of the hump or bulb.
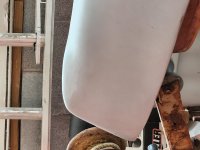
I would use epoxy and fairing compound to make everything appear uniform at the hump or bulb. I would use epoxy to fasten the wooden plank ( the keel and hull strakes) to the hull. I would use ratchet straps to hold these steam bent pieces of wood to the hull while the epoxy cures.
In sum, I would use the ratchet straps to bend the steamed wood and then use the ratchet straps to hold the bent wood onto the hull while the epoxy cured.
Again, is this idea feasible or will the force to bend the steamed wood be too great for ratchet straps to achieve?
Will the wood want to spring back some after bending it so that attempting to epoxy curved wood under the pressure of the ratchet straps be unfeasible?
I am reluctant to screw the wood planks into the hull because of potential leaks. Moreover, the hull is only 5/16ths of the an inch thick. This brings another question to mind.
Would such a hull be strong enough to accommodate the force of tightening down the ratchet straps to bend 1/2 to 3/4 inch thick White Oak?
I believe I have to use wood that has not been kiln dried and I have access to non kiln dried wood.
If it is an unreasonable to steam bend wood with ratchet straps that is O.K.. As I said I have never done this before.
Any insights would be most welcome.
Last edited: