Perhaps this should go into my what's on the workbench thread since it is currently spread out ALL OVER my workbench but I do have some questions.
I was given sometime back a Craftsman 10" Radial Arm Saw. Motor works just fine and for the most part there is just surface rust on the exposed steel parts. Easy enough to deal with. However, the handle to crank the arm up and down to adjust the height of the cut wouldn't rotate. Initially based on what I saw, I thought perhaps it was the shaft of the arm itself that goes into the cast iron sleeve/base was somehow seized to the sleeve. So I Kroiled the bejeezus out of it over the course of a few weeks and it never broke free. So I got to thinking hmmmmmm maybe it's the gears that interact with each other. Last night after finishing putting together my buffing wheel I decided that I would tackle the radial arm saw again. I don't know why I took so long to do it. Jeeesh it is way easier to take apart than many of the guns that I work on every day.
Anyway, I got the gears pulled out and I still couldn't get the arm to release out of the cast iron sleeve (and yeah I know I'm not using the right terms but they escape me right now). So it likely is an issue with the arm shaft and sleeve interface. However the gears could use a little love as well. I will get the gears all cleaned up of any of the crustiness and the little bit of rust that is present but how do I go about removing the arm from the shaft to clean up that interface? I thought about brute force using a come-a-long and anchoring the cast iron sleeve to something and then slowly seeing if I could ratchet it out of the sleeve, but there has to be a better way? I have removed all of the parts associated with the sleeve and shaft I believe.
Though there is a good bit of surface rust on the exposed un painted metal, the innards and the bolts and screws were ALL super easy to remove and for the most part very clean. The rust you see on the gears here is the worst of the internal rust that I have seen.
As you can see in the picture down below, the threaded area is quite clean of rust so there shouldn't have been issues going up and down with that.
And then the removed arm from the table base
I would have thought that if it were a gear interfacing issue that removing the gears would allow the arm to go up and down. I can't get it to budge up or down though so I go back to my initial thought of shaft/sleeve interface issues.
Sooooooooooooo how would y'all do it to get the arm out of the sleeve? Have I missed something as far as taking it all apart?
Once it is ready to be all back together again and cleaned up, before installing.....what kind of grease should I put in/around the gears? It obviously has some and it's old and ooky so a fresh round ought to be good for it. Is wheel bearing grease okay for it or does it need something else?
Thanks a lot again to the brain trust here!!!
Dani
I was given sometime back a Craftsman 10" Radial Arm Saw. Motor works just fine and for the most part there is just surface rust on the exposed steel parts. Easy enough to deal with. However, the handle to crank the arm up and down to adjust the height of the cut wouldn't rotate. Initially based on what I saw, I thought perhaps it was the shaft of the arm itself that goes into the cast iron sleeve/base was somehow seized to the sleeve. So I Kroiled the bejeezus out of it over the course of a few weeks and it never broke free. So I got to thinking hmmmmmm maybe it's the gears that interact with each other. Last night after finishing putting together my buffing wheel I decided that I would tackle the radial arm saw again. I don't know why I took so long to do it. Jeeesh it is way easier to take apart than many of the guns that I work on every day.
Anyway, I got the gears pulled out and I still couldn't get the arm to release out of the cast iron sleeve (and yeah I know I'm not using the right terms but they escape me right now). So it likely is an issue with the arm shaft and sleeve interface. However the gears could use a little love as well. I will get the gears all cleaned up of any of the crustiness and the little bit of rust that is present but how do I go about removing the arm from the shaft to clean up that interface? I thought about brute force using a come-a-long and anchoring the cast iron sleeve to something and then slowly seeing if I could ratchet it out of the sleeve, but there has to be a better way? I have removed all of the parts associated with the sleeve and shaft I believe.
Though there is a good bit of surface rust on the exposed un painted metal, the innards and the bolts and screws were ALL super easy to remove and for the most part very clean. The rust you see on the gears here is the worst of the internal rust that I have seen.
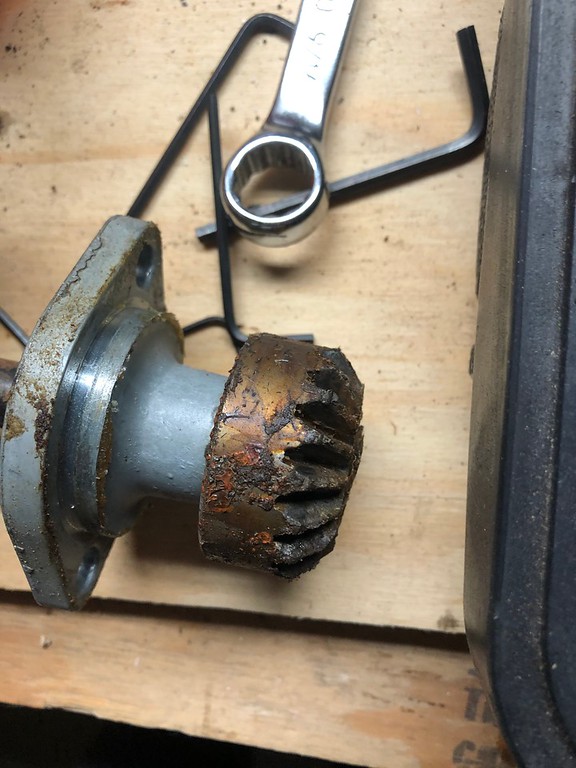

As you can see in the picture down below, the threaded area is quite clean of rust so there shouldn't have been issues going up and down with that.

And then the removed arm from the table base

I would have thought that if it were a gear interfacing issue that removing the gears would allow the arm to go up and down. I can't get it to budge up or down though so I go back to my initial thought of shaft/sleeve interface issues.
Sooooooooooooo how would y'all do it to get the arm out of the sleeve? Have I missed something as far as taking it all apart?
Once it is ready to be all back together again and cleaned up, before installing.....what kind of grease should I put in/around the gears? It obviously has some and it's old and ooky so a fresh round ought to be good for it. Is wheel bearing grease okay for it or does it need something else?
Thanks a lot again to the brain trust here!!!
Dani
Last edited: