I looking for a little advice. I want to add a mud motor but the boat I have is to small for the added weight. It's a Lowe 1440M. I'm considering purchasing pods from Beavertail but I'm concerned about the weldablity of two thicknesses of material. The pods are .100 thick and the hull is .064. Is this a good idea or is there to much risk of burn thru of the thinner hull material in getting a good weld? Also I'm thinking of eliminating the front seat and adding an extention of the front deck for the dog. Any thoughts about welding in this area? I'm leaning towards using .080 or .090 material so I don't get a lot of deflection in the material. Would riveting be a better solution for the added deck area? The front deck will be one piece having a 90 degree bend with a access hole in the front as you would be looking at the deck from the motor.
Thanks,
Ed L.
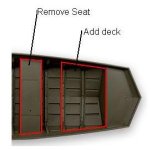
Thanks,
Ed L.
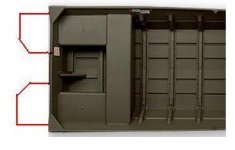
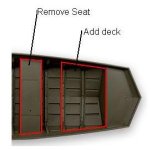