Latest Update:
-Remaining ribs removed
-All flotation foam removed
-Forward ribs installed
-Lots of grinding completed, much more to do..
Originally, I was disappointed to see the top/bottom hull seam separation at the stern, but turns out it will make transom removal much easier. Notice the shim material under the ply transom. They appear to be some kind of synthetic material, maybe resin filler. It's either shims for poor fitment, or possibly a layer to keep the ply off the bottom. Either way the ply layers were not glassed to the transom or otherwise separated from the saturated foam.
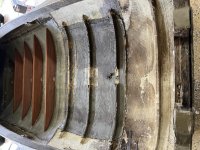

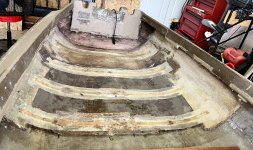
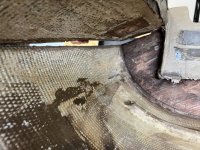
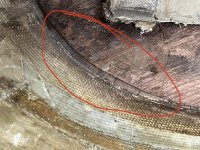
-Remaining ribs removed
-All flotation foam removed
-Forward ribs installed
-Lots of grinding completed, much more to do..
Originally, I was disappointed to see the top/bottom hull seam separation at the stern, but turns out it will make transom removal much easier. Notice the shim material under the ply transom. They appear to be some kind of synthetic material, maybe resin filler. It's either shims for poor fitment, or possibly a layer to keep the ply off the bottom. Either way the ply layers were not glassed to the transom or otherwise separated from the saturated foam.
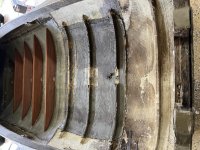

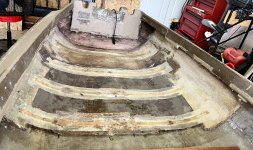
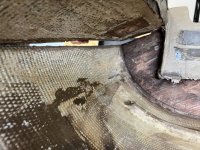
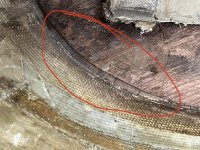
Last edited: