Unless I'm going to flock a decoy I use this surface process whether it's wood or foam. Foam decoys get the typical burlap process, then a 2nd layer of tile adhesive to smooth things up a bit. Wood decoys get a coat of tile adhesive as well to smooth out the wood grain. If I'm going to do the feather detail instead of a flocked decoy I start additional coats of tile adhesive.
I got the idea nearly 15 years ago when I was seeing guys putting texturing paste on wood and cork divers and then combing in the vermiculation. When I tried texturing paste I noticed that it's not much different than tile adhesive. I started out trying to comb the feather lines while the adhesive was still wet, but that wasn't very fast or productive. It didn't take long to figure out that stoning the tile adhesive was going to be the best approach for details on a foamer. It takes several coats of tile adhesive over a burlapped decoy, smoothing it out with a wet brush roughly in the direction of the feathers, probably at least 4 or 5 coats before you have a surface thick enough to detail. It's got to cure a few days before stoning.
I do the same with wood carvings, it helps to avoid sanding. About the only thing I sand by hand is the bill on a wood carving, I mold my own bills from my own carvings for the foamers. For decoys like the ringer, that are expected to hunt I put two coats of high performance gloss oil based enamel from rustoleum as a sealer, it's a bit thinner than regular rustoleum oil base, it soaks into the tile adhesive very well. You can get a ton of detail in a short amount of time with this process.
This full body floating mallard is a foamer.
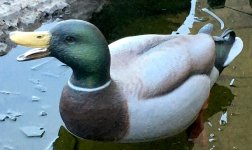
This full size green wing is a wood carving, but surfaced the same way with tile adhesive.
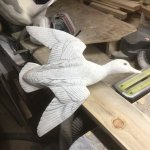
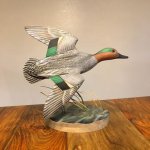