Steve Sanford
Well-known member
All~
Got a few birds to the DONE stage - a few Grey Ducks - but Drakes only thus far.
This Herter's Model 63 came to me as a Mallard (?):
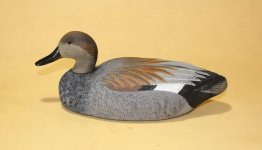
This is an E Allen Gadwall - the first Gadwall I've done from this maker.
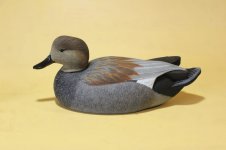
There will be 4 Grey Ducks altogether - and each will get a flush, unballasted keel because they will be used for carry-in hunts on small waters. I have a rig like this - Mallards, Blacks, Woodlies - for small waters hereabouts. Note the 2-ounce bank sinker I use for the "anchor".
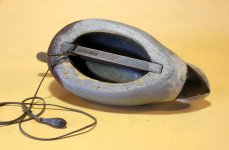
Here are the 2 Drakes in natural light. Their Hens are half-done. It's tough to see in this photo, but I sliced a small wedge off the neck on the starboard bird - to give a slightly different attitude. The port bird - which was the one on the bench - is the stock head.
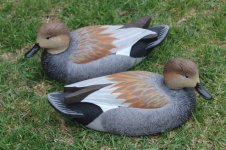
All the best,
SJS
Got a few birds to the DONE stage - a few Grey Ducks - but Drakes only thus far.
This Herter's Model 63 came to me as a Mallard (?):
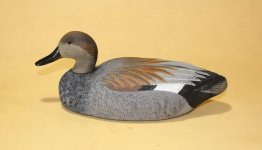
This is an E Allen Gadwall - the first Gadwall I've done from this maker.
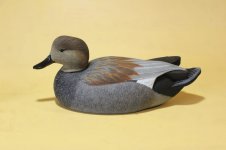
There will be 4 Grey Ducks altogether - and each will get a flush, unballasted keel because they will be used for carry-in hunts on small waters. I have a rig like this - Mallards, Blacks, Woodlies - for small waters hereabouts. Note the 2-ounce bank sinker I use for the "anchor".
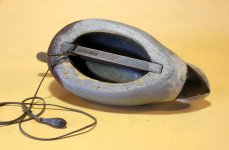
Here are the 2 Drakes in natural light. Their Hens are half-done. It's tough to see in this photo, but I sliced a small wedge off the neck on the starboard bird - to give a slightly different attitude. The port bird - which was the one on the bench - is the stock head.
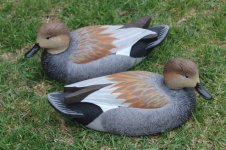
All the best,
SJS